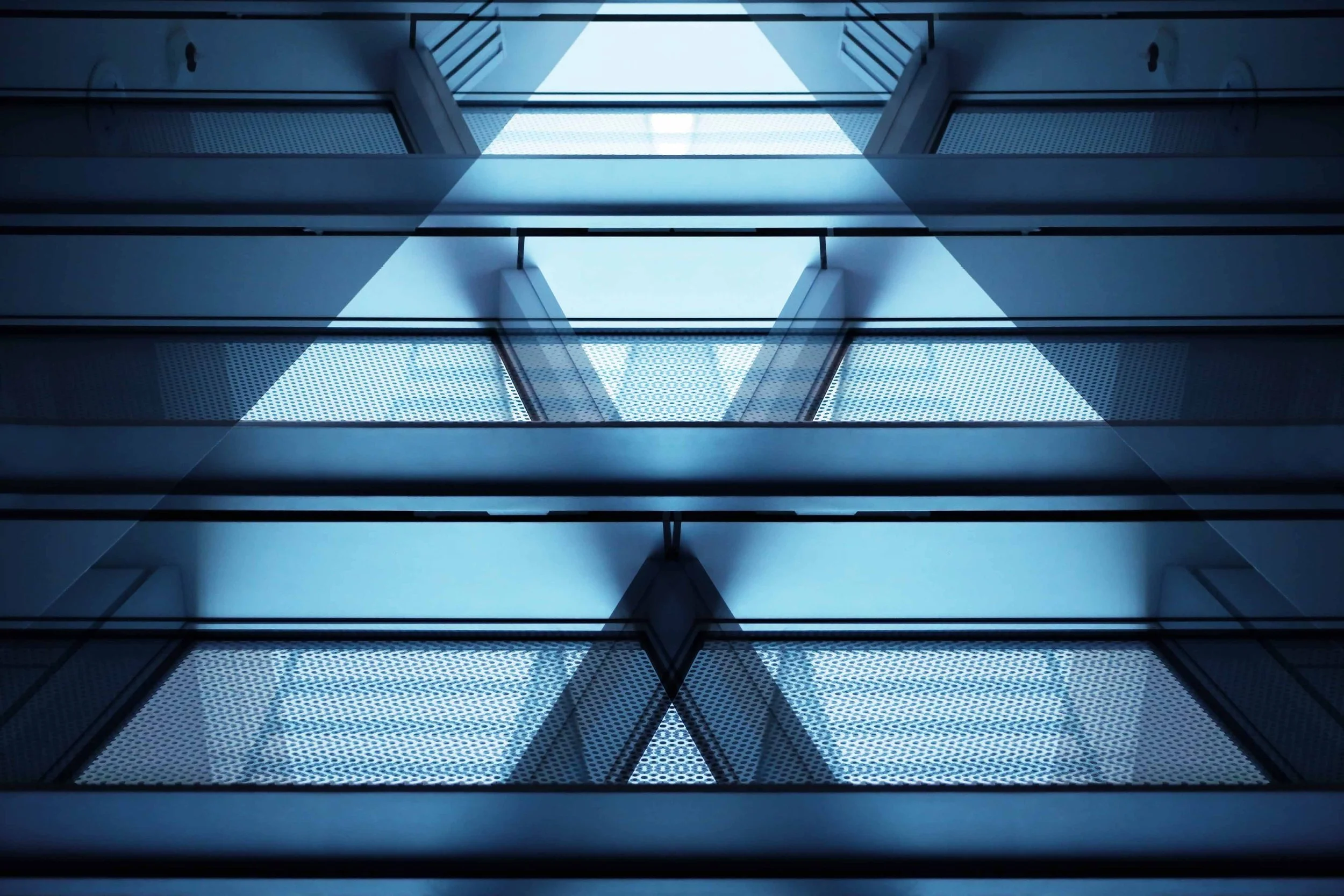
Active Fire UK are a fully accredited and certified provider of fire sprinkler and protection services to both domestic and commercial properties.
The importance of sprinkler systems in residential buildings
As the world is growing rapidly, the construction of residential buildings is increasing at an unprecedented pace. With the increase in the number of buildings, the safety of the residents is of utmost importance. One of the most effective ways to ensure the safety of residents in case of fire is by installing sprinkler systems in residential buildings. Sprinkler systems are not just an optional safety feature; they are essential in protecting life and property.
Sprinkler systems are designed to detect the heat and smoke caused by a fire and to release water immediately. The water from the sprinkler systems can extinguish the fire or at least reduce the intensity of the fire, allowing residents more time to evacuate the building safely. The importance of sprinkler systems in residential buildings cannot be overemphasized, as they have been proven to be effective in reducing the number of fatalities and injuries from fires.
Moreover, sprinkler systems can also prevent the spread of fire to other parts of the building. The fire can be contained in the room where it originated, which can significantly reduce the damage caused by the fire. This means that not only will sprinkler systems save lives, but they can also save property from destruction.
In addition, sprinkler systems are cost-effective in the long run. The cost of installing sprinkler systems may seem high, but it is worth it in the long run. The cost of repairing the damage caused by a fire can be much higher than the cost of installing a sprinkler system. Sprinkler systems can also reduce insurance premiums, as insurance companies recognize the importance of sprinkler systems in reducing the risk of a fire.
The importance of dry risers and wet risers in buildings
In modern architecture, the role of dry risers and wet risers in buildings has become increasingly important. These systems are designed to deliver water to the upper floors of a building in case of a fire emergency. They help firefighters to extinguish the fire quickly and prevent massive damage to the property. In this essay, we will discuss the importance of dry risers and wet risers in buildings and how they can save lives and property.
Dry risers and wet risers are essential firefighting systems in buildings. They are designed to transport water from a ground-level inlet to upper floors of a building in case of a fire emergency. The dry riser system is a pipe that runs through a building with an inlet at the ground level and outlets on each floor.
The wet riser system is similar to the dry riser system, but it has a constant water supply and is pressurized, making it more effective in firefighting. In case of a fire, every second counts. Dry risers and wet risers can provide quick access to water, allowing firefighters to respond to the emergency immediately. For instance, in the Grenfell Tower fire in London, dry risers and wet risers played a crucial role in extinguishing the fire quickly.
Dry risers and wet risers are required by building regulations in many countries. Compliance with these regulations ensures that the building is safe for occupants and firefighters in case of a fire emergency. For example, in the UK, every building over 18 meters tall must have a dry riser system installed covered in BS9990.
Our Services
Automatic Sprinkler System Maintenance
-
Active Fire UK provide a full service and maintenance offering to our clients.
Under The Regulatory Reform (Fire Safety) Order 2005 it is a legal requirement to maintain your building’s sprinkler system in the UK. It is important to follow the guidelines set out in the British Standard BS 9251:2014.
-
Here are some general steps we will take to maintain your sprinkler system:
1. Regular inspections
Conduct frequent inspections of the sprinkler system to detect any signs of damage or wear and tear on any aspect of the system. You must contract a qualified engineer to do it for you. It is recommended that inspections are carried out at least once a year, but it may be more frequent depending on the system's age, location, and usage.2. Testing
Regularly test the system to ensure that it is working correctly. This should involve activating the sprinkler system to check that the water flow is adequate and all the sprinkler heads, flow switches and valves etc are functioning correctly.3. Keep the area around the sprinkler system clear:
Ensure that the area around the sprinkler system is clear of any obstructions that could affect the system's performance. This includes removing any flammable materials or objects that could ignite in the event of a fire.4. Check the water supply
Ensure that the water supply to the sprinkler system is properly maintained and tested. This includes checking the pressure, flow rate, and water quality.5. Record keeping
Keep records of all inspections, tests, and maintenance activities carried out on the sprinkler system. This is important for compliance and can also help identify any areas that may require additional attention.It's important to note that maintenance requirements may vary depending on the type of sprinkler system installed, so it's always best to consult with a qualified professional for specific maintenance instructions.
Dry & Wet Riser Maintenance
-
Dry risers and wet risers are both fire protection systems that help firefighters to deliver water to upper floors of tall buildings in case of fire. The main difference between dry risers and wet risers is the way in which they are filled with water.
Dry risers are empty pipes that are kept dry and are only filled with water when needed. Water is supplied to the dry riser system by the fire department or by a water storage tank or pump. When needed, firefighters connect their hoses to the dry riser and pump water up to the upper floors of the building. Dry risers are usually installed in buildings over 18m tall.
On the other hand, wet risers are pipes that are kept permanently filled with water. They are connected to a pressurized water supply system, such as a water tank or pump, which ensures that water is always available in the riser. When needed, firefighters connect their hoses to the wet riser and access water from the system. Wet risers are typically installed in buildings over 50m tall.
-
Dry risers require wet testing at least once per year and a visual inspection at least every 6 months as per BS9990:2015. Active Fire UK offer both of these services which are outlined below:
Major Service:
1. Ensure all outlet valves are closed and inspect for any damage, corrosion or blockage to valves and/or cabinets.
2. If any parts are damaged, worn or missing these will be replaced.
3. Ensure access to dry riser points are kept clear and accessible at all times.
4. Pressure test to 12 bar for 15 minutes by filling riser system with water and monitoring pressure gage to ensure there are no leaks and/or pressure loss.
5. If pressure test passes, empty the dry riser of water.
6. Testing report provided for your insurance records.
Minor Service:
1. Ensure all outlet valves are closed and inspect for any damage, corrosion or blockage to valve and/or cabinet.
2. If any parts are damaged, worn or missing these will be replaced.
3. Ensure access to dry riser points are kept clear and accessible at all times.
4. Testing report provided for your insurance records.
Wet risers require testing at least once per year as per BS9990:2015. Active Fire UK offer this service as outlined below:
1. Inspect for any damage, corrosion or blockage to valves and/or cabinets.
2. If any parts are damaged, worn or missing these will be replaced.
3. Static pressure test of outlet points include taking pressure readings at each landing valve.
4. Check internal cleanliness of storage tanks.
5. Thorough check of pumps and their associated water supplies.
6. Testing report provided for your insurance records.
Quarterly & Annual Hazard Reviews
-
Quarterly and annual hazard reviews are part of the regular maintenance and testing requirements for automatic sprinkler systems in the UK.
-
Here are the general steps for quarterly and annual hazard reviews:
1. Identify potential hazards
Conduct a review of the building or area being protected by the automatic sprinkler system to identify any potential hazards that may have emerged since the last review. This includes identifying any changes in occupancy, use of the building, storage of goods, or any other changes that may affect the sprinkler system's effectiveness.2. Review the system design
Review the automatic sprinkler system's design to ensure that it's still appropriate for the current hazard classification of the building or area. This includes reviewing the sprinkler head coverage, water supply, and pressure requirements.3. Review system documentationReview the automatic sprinkler system's documentation, including the hazard analysis, hydraulic calculations, and other relevant documentation, to ensure that they are up to date and accurate.
4. Identify required changes
Identify any required changes to the automatic sprinkler system or its documentation based on the review findings. This may include changes to the sprinkler heads, pipes, valves, or water supply.5. Make necessary changes
Make any necessary changes to the automatic sprinkler system or its documentation based on the review findings. This may include making changes to the sprinkler heads, pipes, valves, or water supply.It's important to note that quarterly and annual hazard reviews may vary depending on the type of automatic sprinkler system installed and the building's hazard classification, so it's always best to consult with a qualified professional for specific review instructions. Regular hazard reviews can help ensure the effectiveness of the automatic sprinkler system in protecting your property and people in the event of a fire emergency.
Fire Hydrants & Hose Reels
-
Fire hydrants and hose reels are essential components of fire protection systems in the UK. Proper maintenance of fire hydrants and hose reels can ensure that they are ready to use in case of a fire emergency.
-
Here are the general steps for fire hydrants and hose reels maintenance:
1. Inspect fire hydrants and hose reels regularly
Inspect fire hydrants and hose reels regularly to detect any signs of damage or wear and tear. This includes checking for leaks, cracks, or other visible signs of damage.2. Test the water supply
Test the water supply to the fire hydrants and hose reels regularly to ensure that the pressure and flow rate are adequate. This includes testing the water pressure at the hydrant or reel and checking the water quality.3. Keep the area around fire hydrants and hose reels clear
Ensure that the area around the fire hydrants and hose reels is clear of any obstructions that could affect their use. This includes removing any vehicles or other obstacles that may block access to the hydrant or reel.4. Maintain records
Keep records of all inspections, tests, and maintenance activities carried out on the fire hydrants and hose reels. This is important for compliance and can also help identify any areas that may require additional attention.5. Carry out repairs and replacements
If any damage or issues are identified during inspections or testing, carry out the necessary repairs or replacements promptly to ensure that the fire hydrants and hose reels are ready to use in case of a fire emergency.It's important to note that fire hydrants and hose reels maintenance requirements may vary depending on the specific fire protection system installed, so it's always best to consult with a qualified professional for specific maintenance instructions. Regular maintenance and testing of fire hydrants and hose reels can help ensure their effectiveness in protecting your property and people in the event of a fire emergency.
25 Year Testing
-
25-Year testing on sprinklers in the UK refers to the requirement for automatic sprinkler systems to undergo a full test and inspection every 25 years to ensure their continued effectiveness in preventing and controlling fires.
-
Our testing includes Lab Sprinkler Head Testing, Pipework & Waterway Inspections and Pipework Flushing, all in accordance with the British Standard BS 9251:2014, which sets out the design, installation, and maintenance requirements for residential and domestic sprinkler systems. The testing must be carried out by qualified and certified sprinkler engineers or contractors.
Water Storage Tanks
-
Water storage tanks are used for sprinkler systems to ensure that there is an adequate water supply available to operate the system in case of a fire emergency. The water storage tanks are typically large containers that hold a significant amount of water, depending on the size of the building or area being protected.
When a sprinkler system is activated during a fire, the water is released from the storage tank and flows through the pipes to the sprinkler heads. The water pressure and flow rate is regulated and controlled by the sprinkler system's control valve.
Water storage tanks are important for ensuring that the sprinkler system has enough water to effectively suppress the fire until the fire brigade arrives. They can be installed above ground or below ground, depending on the available space and the building's design. The size and capacity of the water storage tank are determined by the building's hazard classification and the sprinkler system's design.
-
Water storage tanks for sprinkler systems require regular inspections, cleaning, and maintenance to ensure that they are functioning properly and to prevent contamination of the water supply. Regular testing and inspections of the tank's valves, piping, and fittings are also recommended to ensure that the system is ready to be used in case of an emergency.
Fire Pumps
-
Fire pump maintenance is an essential aspect of maintaining an automatic sprinkler system in the UK.
-
Here are the general steps for fire pump maintenance:
1. Regular inspections
The fire pump should be inspected at least once a year to detect any signs of wear and tear, corrosion, or damage. The inspection should include the pump, motor, and driver.2. Testing
The fire pump should also be tested to ensure that it's working correctly. This should involve testing the pump's flow rate, pressure, and performance under different conditions.3. Keep the area around the fire pump clear
Ensure that the area around the fire pump is clear of any obstructions that could affect the system's performance. This includes removing any flammable materials or objects that could ignite in the event of a fire.4. Check the water supply
Ensure that the water supply to the fire pump is properly maintained and tested. This includes checking the pressure, flow rate, and water quality.5. Maintain records
Keep records of all inspections, tests, and maintenance activities carried out on the fire pump. This is important for compliance and can also help identify any areas that may require additional attention.It's important to note that fire pump maintenance requirements may vary depending on the type of automatic sprinkler system installed, so it's always best to consult with a qualified professional for specific maintenance instructions. Regular maintenance and testing of a fire pump can help ensure the effectiveness of the automatic sprinkler system in protecting your property and people in the event of a fire emergency.
Free Consultation
-
Unsure of your responsibilities and the requirements surrounding your building's active fire protection systems? Get in touch with us today. We provide free, expert advice!
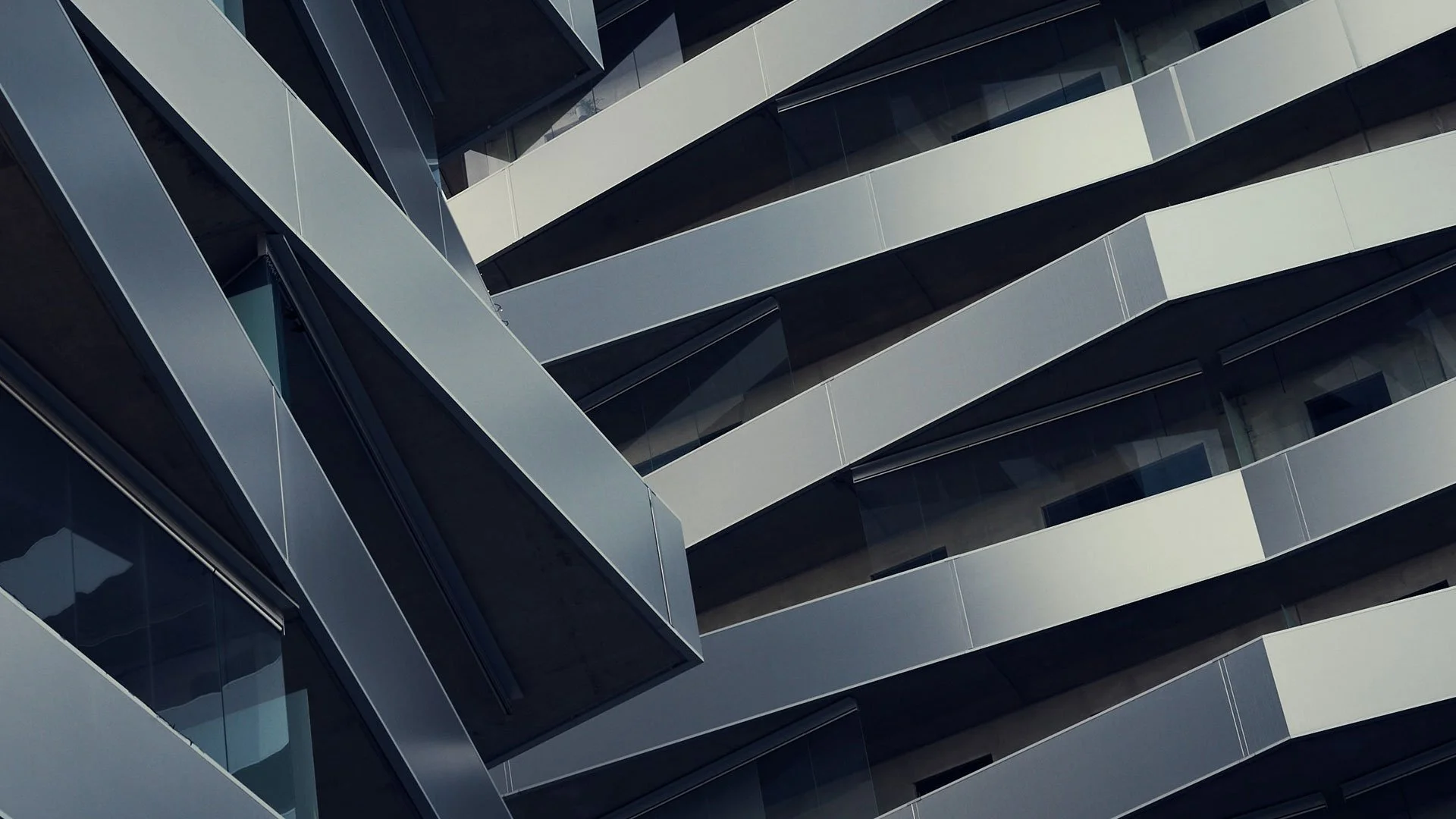
– What we stand for –
Our values are integral to our service mission. By following our values, our team can be confident that their work is of a consistent, exemplary standard. Moreover, our values enable us to continually improvement, making processes simpler and more cost effective without sacrificing quality.
Contact us.
If you have any questions or comments, please contact us via email or phone, or send us a message using the contact form.
Phone
+44 (0) 203 886 0223